-
3-3
PZU takes initiatives to reduce consumption of raw materials, i.e. water and paper in particular. The second aspect of environmental initiatives is the proper disposal of equipment set for decommissioning.
Paper
PZU takes measures to switch from paper communication to electronic one. These measures have a particular impact on sending motor and agricultural insurance renewals. In 2022, one in four clients received renewal communication electronically. This represents an annual savings of 7.6 million zlotys in the cost of materials, printing service and mailing.
-
301-1
Total consumption of raw materials in the PZU Group
In 2022, 72% of the insurance forms in terms of the weight are prepared on certified paper – this result is for both companies (78% in PZU and 61% in PZU Życie). In 2023, the commitment to have at least 50% of the insurance forms in terms of the weight prepared on certified paper, will be continued. All new printing devices have the Blue Angel certificate are equipped with an automatic two-sided printing (duplex) module – wherever the specific nature of work permits two-sided printing, it is set as the default printing option.
PZU and PZU Życie systematically reduce the purchase and consumption of office supplies, including paper, constantly reducing the number of printers used. In 2022, paper was purchased from a paper mill located in Poland, minimizing the carbon footprint of transporting paper. Additionally, the Discovery paper is produced from the Blue Gum eucalyptus tree which, thanks to a different fiber structure, makes it possible to reach a ca. 37% reduction of the wood used in relation to the commonly used trees, such as maritime pine or paper birch.
-
301-1
Total consumption of raw materials in PZU and PZU Życie
PZU | PZU Życie | |||
---|---|---|---|---|
2021 | 2022 | 2021 | 2022 | |
Paper [t] | 119 | 114 | 78 | 85 |
Paper consumption at PZU and PZU Życie
Year | Paper/tons | Change |
---|---|---|
2017 | 290 | – |
2018 | 277 | -4.6% |
2019 | 276 | -0.3% |
2020 | 204 | -26.1% |
2021 | 197 | -3.4% |
2022 | 199 | 1.0% |
Reduction of the number of printers at PZU and PZU Życie
The volume of used mobile phones and modems to be recycled and sold to company employees
Year | Quantity (pcs.) |
---|---|
2018 | 2,602 |
2019 | up to 2,030 |
2020 | over 3,000 |
2021 | 1,703 |
2022 | 1,046 |
Reduction of the number of printers at PZU and PZU Życie
Year | Number of printing devices remaining in operation at the end of th e calendar year in question |
Reduction |
---|---|---|
2017 | 5,000 | – |
2018 | 4,750 | 5.0% |
2019 | 4,600 | 3.2% |
2020 | 4,540 | 1.3% |
2021 | 4,420 | 2.6% |
2022 | 4,290 | 2.9% |
Best practices of subsidiaries
The PZU Group companies cooperate with firms offering the highest waste management standards, confirmed by pertinent environmental certificates. PZU and PZU Życie set their goal to increase recycling in the total number of liquidated assets. In 2023, there is a plan to continue recycling in the total number of liquidated assets should increase again. This ratio is achieved by promoting the sale of assets to employees, external clients or by donating them. Additionally, collections of used mobile phones are held regularly and the devices are sold to a specialized company (recycling).
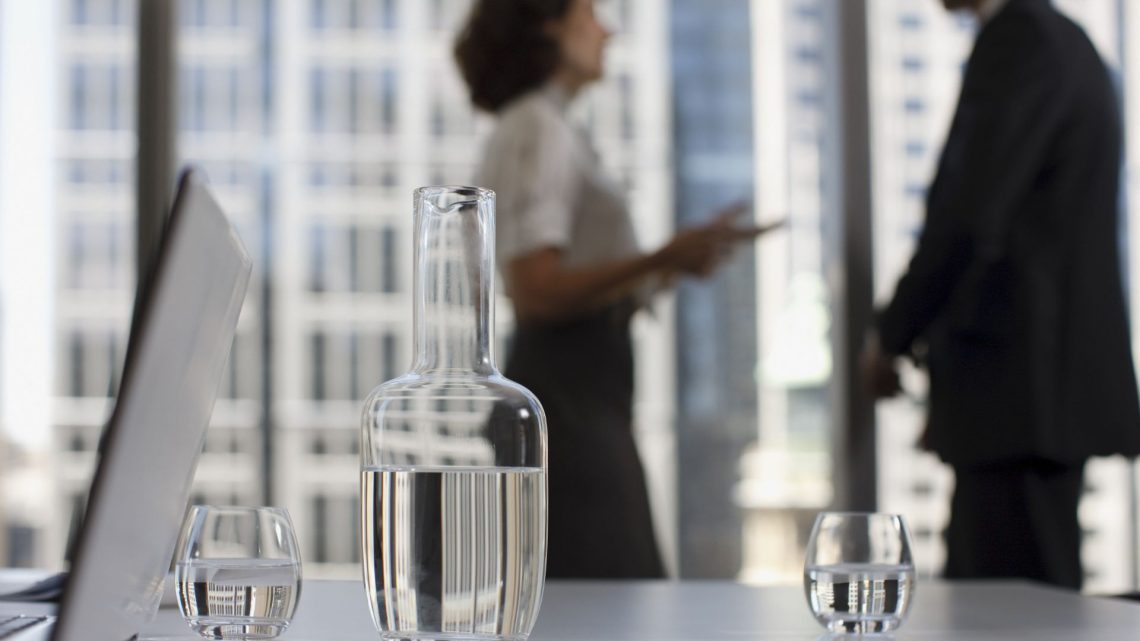
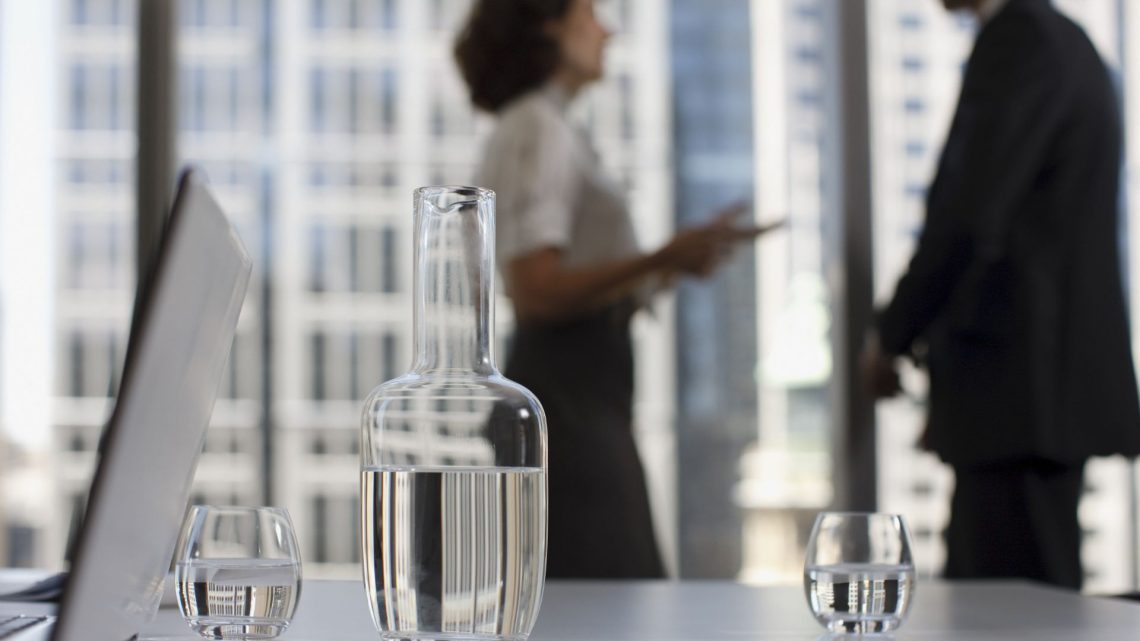
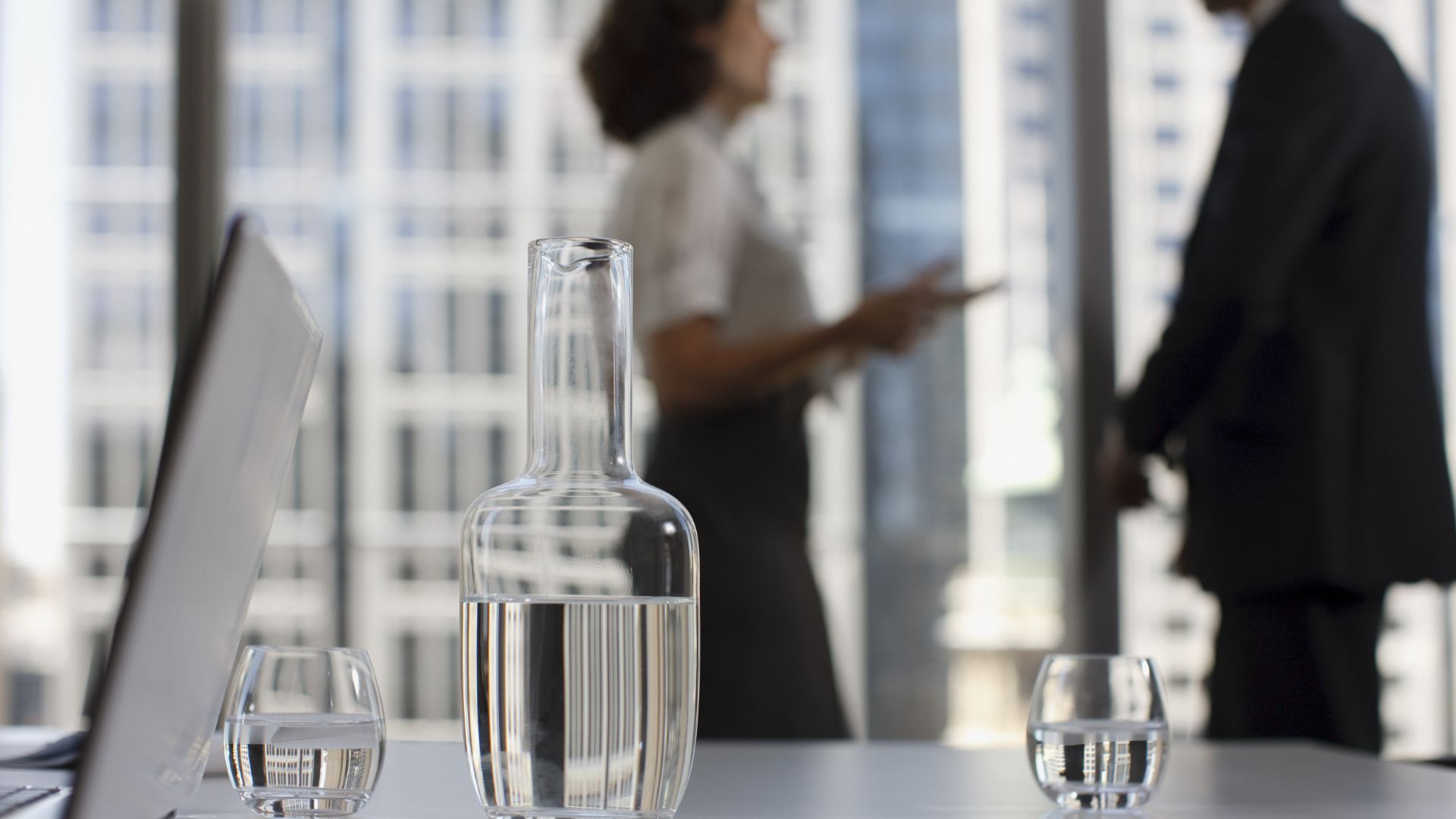
Water
Reduction initiatives
Water saving activities are associated largely with distribution of potable water. Since 2018, PZU has been implementing a change in the distribution of water in big plastic bottles to a more sustainable system. Installation of water dispensers using water from the water supply system, use of running water filters or consumption of water directly from the tap in places where water is good to drink, not only optimizes the use of water but also reduces the number of plastic bottles on the market, reduces carbon emissions by eliminating transport and reduces the energy and raw materials needed to manufacture plastic bottles.
In Q3 2022, Armatura Kraków implemented an efficient system for cooling the water circuit in preparation for painting a radiator, using a chilled water system (chiller). The new solution will save an average of 4,000 m³ of water per year. Water consumption savings depend on weather conditions of the year and air temperatures.
The offer of KFA Armatura also covers a faucet series with reduced water consumption (down to a level of 5-6 l/min). Traditional kitchen and sink faucets consume 12 l/min. Faucets offered by KFA Armatura use half as much water, i.e. 5-6 l/ min. In 2022, over 20,000 units of water-saving faucets were sold, including those from the Moza, Logon, Mokait, Abasha collections.
The company’s portfolio also includes the Mungo Faucet with water filtration function. The Mungo Faucet supports users’ ecological attitudes and influences the reduction of the use of plastic water bottles. The filter cartridge for the faucet is installed directly under the sink, and one filter lasts for 6,000 liters of water or a period of 6 months.
The KFA Armatura brand is conducts an extensive educational project on water conservation. In 2022, its green communication activities reached more than 600,000 users.
-
303-5
Total consumption of water in the PZU Group
PZU Group | 2021 | 2022 |
---|---|---|
Water [m3] | 272,837 | 285,117 |
-
303-5
Total consumption of water in PZU and PZU Życie
PZU | PZU Życie | |||
---|---|---|---|---|
2021 | 2022 | 2021 | 2022 | |
Water [m3] | 37,397 | 38,815 | 14,311 | 16,012 |
Planned reduction in the number of water dispensers and big water bottles*
Year (end) | Number of dispensers per big bottle | Number of big bottles | Change in the number of dispensers (y/y) |
---|---|---|---|
2018 | 1,145 | 4,665 | – |
2019 | 916 | 3,732 | -20% |
2020 | 733 | 2,986 | -20% |
2021** | 738 | 3,533 | 0.7% |
2022*** | 117 | 1,353 | -84% |
** The increase in the number of big bottle dispensers by 5 units from 2020 is due to increased demand for water as employees returned to stationary work and tap dispenser failures. Starting on 1 April 2022, big bottle dispensers will be gradually replaced with tap water dispensers.
*** A tender procedure for tap water dispensers was commenced in 2021 throughout the entire country at the same time. A new agreement for dispensers was concluded. After the agreement is implemented, the big bottle dispenser will remain only in the facilities where they cannot be connected to the water system due to technical or ownership reasons.


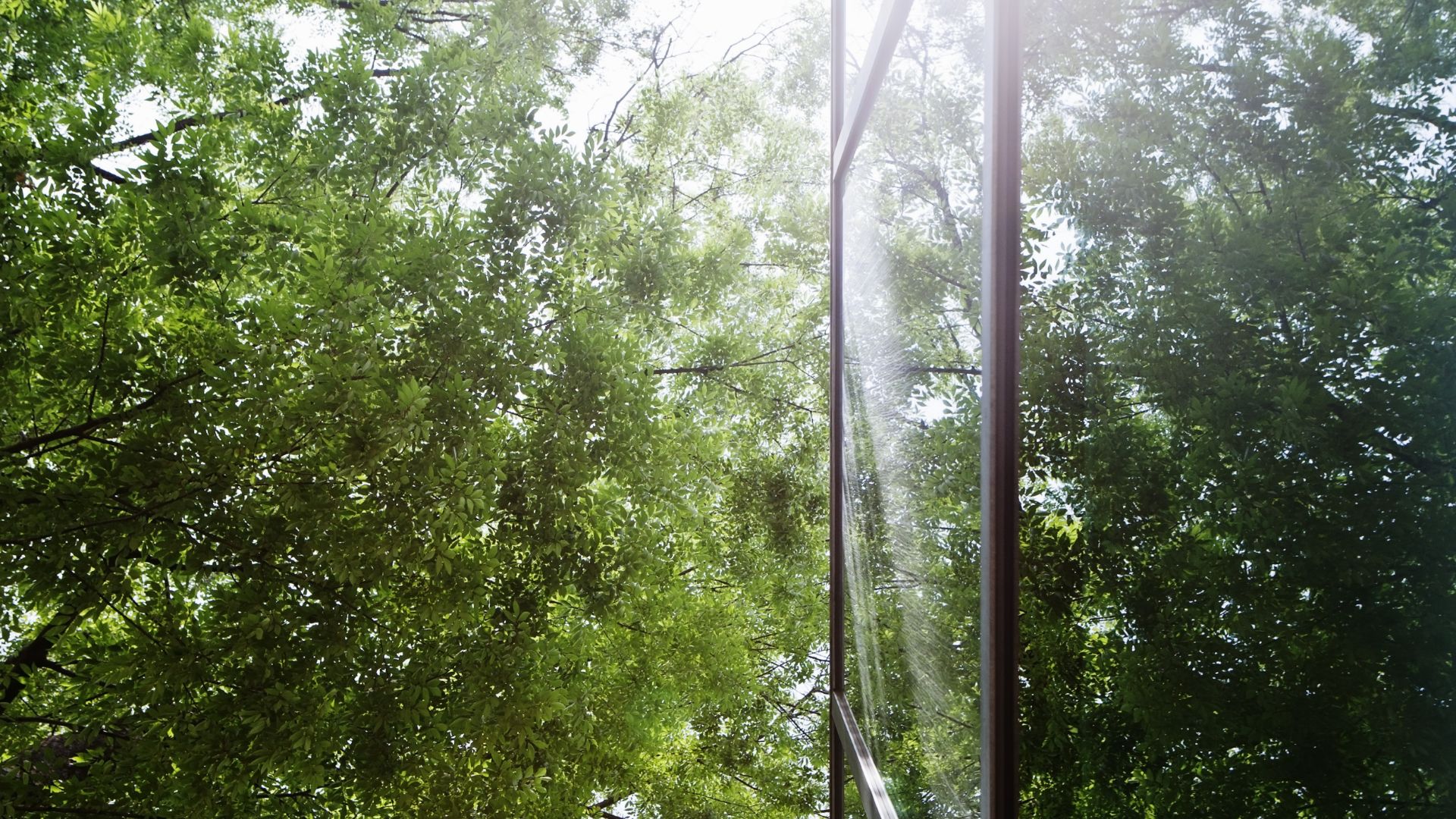
Assets for decommissioning
In 2022, 15.2 thousand assets (including telephones) set for decommissioning were resold (to employees and external clients), which accounts for more than 53% of liquidated assets. More than one thousand assets were donated to schools, foundations, fire departments and others in need, including telephones, white goods - coffee makers, refrigerators, dishwashers, microwaves, LCD TVs, LCD large format displays/monitors, shredders, projectors, small office equipment.
2022 | Quantity (units) | % share |
---|---|---|
Disposal | 12,480 | 43.4% |
Sale | 15,249 | 53.1% |
Donation | 1,009 | 3.5% |
Total decommissioning | 28,738 | 100.0% |
PZU conducts a number of activities to support recycling of computer equipment. By forming responsible attitudes among employees in caring for entrusted assets, some of the decommissioned equipment use can be reused in other areas, resold or donated to public benefit institutions. In 2017-2019, this accounted for an average of 25% of the decommissioned equipment. IT operations always strive to support business objectives of PZU. Therefore, in support of the requirements of hybrid work, which has become a major business objective due to the COVID-19 pandemic and problems with regular supply chains, current employee resale processes were halted in 2020. This made it possible for employees previously not equipped with mobile work tools to work remotely. This approach enabled an almost immediate transition to a new work model, providing security for employees of PZU. Current business needs are also being analyzed and some of them are implemented through internal movement and resale. This increases the efficiency of equipment use and minimizes the environmental cost of producing these devices. Decommissioned equipment is withdrawn on the basis of dedicated agreements with companies implementing handling recycling of equipment and its components.
Alior Bank continued the NFO (New Branch Format) project, increasing the number of branches in under the green format. The Branches were arranged with materials and products from local suppliers. Most of such products were recycled. Examples include countertops made from recycled yogurt cups, upholstery and ceilings made from recycled PET bottle material. In addition, some of the furnishings were made from wood from fast-growing plants. Certified environmentally friendly biodegradable cups are available to customers.
As part of waste management, the Pekao Bank regularly hands over paper documentation, computer media, furniture, and white and brown goods for specialized disposal. The products are recycled and prepared for reuse as raw materials or alternative fuel. When ordering new white and brown goods, the company takes into account the service involving collection and disposal of old goods.